How a MAP Fertilizer Line Can Reduce Waste and Increase Profits in 5 Steps
In the modern agricultural sector, maximizing efficiency and reducing waste is crucial for both environmental sustainability and financial growth. A MAP Fertilizer Line, short for Mono-Ammonium Phosphate fertilizer production line, offers an innovative solution to accomplish both goals. By streamlining production processes, improving product quality, and minimizing waste, businesses can significantly increase their profitability while reducing environmental impact. In this, we’ll explore five key steps to optimize the MAP Fertilizer Line and achieve these goals.
What Is the MAP Fertilizer Line?
Mono-Ammonium Phosphate (MAP) is a high-quality phosphate fertilizer that plays a vital role in crop production. LANE Group’s MAP Fertilizer Line is designed to streamline the manufacturing of this essential fertilizer, enabling agricultural producers to achieve superior crop yields. With high phosphorus and nitrogen content, MAP fertilizer is a popular choice for farmers worldwide, and LANE Group’s innovative production line enhances the overall process, ensuring consistency and quality in every batch.
Precision in Raw Material Handling
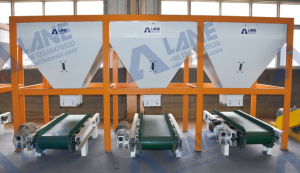
Dynamic Batching System
One of the most significant contributors to waste in fertilizer production is inefficient handling of raw materials. In traditional systems, improper measurement, mixing, and storage can lead to material losses, decreased product quality, and increased costs. However, with a modern MAP Fertilizer Line, precision handling technology ensures that raw materials like phosphate, ammonia, and other additives are measured and mixed with exact accuracy.
Automated weighing and mixing systems integrated into the MAP Fertilizer Line can reduce human error, ensuring consistent quality and minimizing waste. These systems also optimize the use of resources by reducing overuse and eliminating underutilization of valuable materials. The result is a more efficient operation with less waste and higher profits.
Advanced Granulation Technology
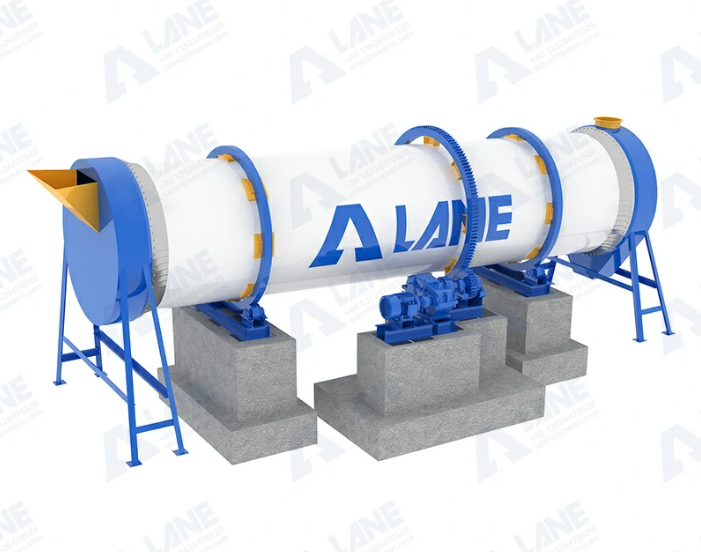
Rotary Drum Granulator
Granulation is a critical step in the fertilizer production process, as it determines the size, shape, and consistency of the final product. Traditional methods often result in inconsistent granules, leading to uneven nutrient distribution when the fertilizer is applied in the field. This can reduce the effectiveness of the fertilizer and increase the likelihood of nutrient run-off, contributing to environmental pollution.
A modern MAP Fertilizer Line is equipped with advanced granulation technology that produces uniform granules of consistent size. This uniformity improves the effectiveness of the fertilizer in the field, reducing the amount required for application. As a result, farmers need less product to achieve the same results, lowering production costs and reducing waste.
In addition, the granulation process in the MAP Fertilizer Line ensures that the fertilizer is more easily stored and transported, further cutting down on logistical waste and expenses.
Energy-Efficient Drying Systems
Drying is another essential phase in the production of MAP fertilizers. Traditional drying methods often consume large amounts of energy, driving up operational costs and contributing to environmental degradation. However, with the incorporation of energy-efficient drying systems in the MAP Fertilizer Line, manufacturers can significantly reduce their energy consumption.
Energy-efficient dryers, such as fluidized bed dryers and rotary drum dryers, are designed to maximize heat transfer and minimize energy loss. These systems can process large quantities of fertilizer at lower temperatures, reducing fuel consumption and CO2 emissions. By adopting an energy-efficient MAP Fertilizer Line, companies not only cut energy costs but also enhance their sustainability credentials, appealing to eco-conscious consumers and regulatory bodies.
Furthermore, the precise control offered by modern dryers ensures that the moisture content of the final product is consistent, which improves the storage stability and shelf life of the fertilizer. This prevents spoilage and waste due to improper drying and storage conditions.
Automated Packaging and Distribution
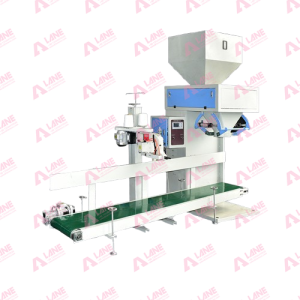
Single Granule packing machine
In any fertilizer production line, the packaging process can be a significant source of waste if not properly managed. Spillage, inaccurate filling, and damaged packaging can lead to product loss and increased costs. The MAP Fertilizer Line combats these issues through the use of automated packaging systems that reduce human error and ensure the accurate filling of bags or containers.
Automated packaging systems in the MAP Fertilizer Line are designed to handle the product with care, minimizing damage to the granules and ensuring that each package is properly sealed to prevent contamination. Additionally, these systems can be calibrated to provide the exact quantity of fertilizer needed for each market, further reducing waste.
Moreover, optimized distribution logistics enabled by integrated software solutions in the MAP Fertilizer Line reduce the carbon footprint associated with transportation. By analyzing shipping routes and load capacities, companies can reduce fuel consumption and delivery times, leading to higher efficiency and lower transportation costs.
Waste Recycling and Byproduct Utilization
One of the most impactful steps toward reducing waste in fertilizer production is the recycling of byproducts. The MAP Fertilizer Line is designed with waste recovery systems that capture and recycle materials that would otherwise be discarded. For example, excess ammonia and phosphate that are not used in the primary production process can be collected, purified, and reintroduced into the system.
In addition to recovering raw materials, the MAP Fertilizer Line can also recycle heat energy generated during the production process. This captured heat can be redirected to other areas of the facility, such as the drying or granulation phases, reducing overall energy consumption.
Another significant advantage of the MAP Fertilizer Line is its ability to turn certain byproducts into valuable products. For instance, excess materials from the production process can be used to create supplementary fertilizers or soil conditioners, generating an additional revenue stream and further minimizing waste.
The Financial and Environmental Benefits of an Optimized MAP Fertilizer Line
By implementing these five steps—precision in raw material handling, advanced granulation technology, energy-efficient drying, automated packaging, and waste recycling—manufacturers can dramatically reduce waste while increasing profitability. The MAP Fertilizer Line is a critical tool in achieving these goals, offering both financial benefits and environmental advantages.
With waste reduction comes cost savings. Companies that utilize a MAP Fertilizer Line experience lower operational costs, including reduced raw material waste, energy consumption, and transportation expenses. At the same time, they can enhance the quality of their product, leading to higher customer satisfaction and loyalty.
Moreover, reducing waste through the MAP Fertilizer Line has a positive environmental impact. By using fewer resources and minimizing emissions, manufacturers can reduce their ecological footprint and contribute to global sustainability efforts. This not only improves public perception but can also position the company to benefit from government incentives or certifications that reward eco-friendly practices.
Conclusion
In today’s competitive agricultural market, finding ways to increase profits while minimizing waste is essential for long-term success. The MAP Fertilizer Line offers a comprehensive solution to achieve both goals. Through precision, energy efficiency, and innovation, companies can produce high-quality fertilizer with minimal environmental impact. By following the five steps outlined in this article, manufacturers can optimize their MAP Fertilizer Line, reduce waste, and boost profits—leading to a more sustainable and successful business model.
Ready to transform your fertilizer production and boost profits with an advanced MAP Fertilizer Line? Contact us today to learn how our tailored solutions can meet your specific needs and take your business to the next level!
Latest Articles & Tips
More-
03/14
OEM Fertilizer Equipment Manufacturing: Custom Solutions for Your Production Needs
read more -
02/27
Fertilizer Granulation for DAP and MAP: Enhancing Efficiency in Fertilizer Production
read more -
02/27
Fertilizer Production Solutions: Optimizing Efficiency and Sustainability in Fertilizer Manufacturing
read more -
02/13
Chemical Fertilizer Production Line: Enhancing Agricultural Productivity with Precision Manufacturing
read more
Send a message to us