How to Optimize Raw Material Mixing for Higher Output in SSP Production
The efficiency of the production process for Single Superphosphate (SSP) fertiliser is contingent upon the quality of the raw material mixing. A well-optimised mixing process will result in superior chemical reactions, reduced waste, and increased production efficiency.
SSP production involves the chemical reaction of phosphate rock with sulphuric acid to produce calcium phosphate and gypsum. The efficiency of this reaction is affected by the proportion, mixing and consistency of the raw materials. Poor mixing can result in incomplete reactions, reducing yield and efficiency. By optimising mixing parameters, manufacturers can ensure higher output in SSP production.
Key Raw Materials for SSP Production
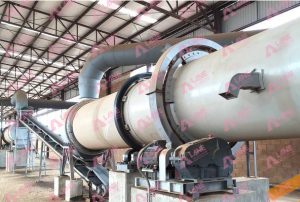
SSP Fertilizer Production Line
- Phosphate Rock
- Supplies phosphorus content essential for fertilizer.
- Quality and particle size distribution affect the mixing efficiency.
- Sulfuric Acid (H₂SO₄)
- Drives the chemical reaction to produce calcium phosphate.
- Precise acid concentration is crucial for balanced reactions.
- Water
- Ensures proper hydration for the chemical reaction.
- Helps maintain the right slurry consistency for granulation.
Strategies to Optimize Raw Material Mixing
Use of Advanced Mixing Equipment
Choosing the right mixing equipment can have a dramatic effect on higher output in SSP production. Modern high-speed mixers and paddle mixers provide better homogenisation of raw materials compared to traditional batch mixers. Automated systems that control the flow of ingredients ensure that the correct proportions are maintained throughout production.
- Benefit: Reduces production downtime by ensuring continuous mixing.
- Effect: Improves production speed, contributing to higher output.
Precise Ratio Control of Raw Materials
Maintaining the correct ratio of phosphate rock to sulphuric acid is essential. An imbalance can lead to incomplete reactions, reducing product yield and quality. Incorporating sensors and automated dosing systems ensures that the mixing process achieves the optimum ratio every time.
- Optimal Ratio: The ideal phosphate rock-to-sulfuric acid ratio ranges from 2.5:1 to 3:1, depending on the rock composition.
- Impact: Proper ratio control leads to more efficient chemical reactions, ensuring higher output in SSP production.
Uniform Particle Size Distribution
The particle size of phosphate rock has a significant effect on mixing and reaction efficiency. Smaller particles increase the surface area, allowing better acid penetration and faster reactions. Sieving and pre-grinding the phosphate rock can ensure uniform particle distribution.
- Impact: Uniform particle size enhances reaction consistency, promoting higher output in SSP production.
Temperature Control During Mixing
Mixing and reacting phosphate rock with sulphuric acid generates heat. Excessive heat can cause clumping of material, reducing mixing efficiency. On the other hand, low temperatures slow down the reaction process, negatively impacting productivity. Maintaining an optimum temperature range of 70°C to 80°C ensures efficient material mixing and chemical reactions.
- Impact: Stabilizing temperature improves reaction speed, resulting in higher output in SSP production.
Use of Additives to Improve Consistency
Incorporating anti-caking agents and flow improvers can help prevent lumping during mixing. These additives ensure that the raw materials remain free flowing and improve their interaction during the blending process.
- Additives Used: Gypsum or silica is often added to maintain the flowability of the mix.
- Effect: Better flow improves mixing efficiency and reduces production downtime, contributing to higher output in SSP production.
Automated Process Monitoring Systems
The implementation of automated monitoring systems ensures that every aspect of the mixing process – temperature, raw material ratios and acid concentration – remains within specified parameters. Real-time adjustments can be made to maintain optimum mixing conditions.
- Impact: Automated systems reduce human errors, ensuring consistent production and higher output in SSP production.
Best Practices for Higher Output in SSP Production
- Pre-treat Raw Materials: Grind phosphate rock to an appropriate size to improve mixing efficiency.
- Monitor Raw Material Quality: Use high-purity phosphate rock and sulfuric acid to ensure consistent chemical reactions.
- Regular Equipment Maintenance: Keep mixers, grinders, and feeders in optimal condition to avoid production delays.
- Optimize Acid Addition: Slowly introduce sulfuric acid to avoid sudden heat spikes during the reaction.
Optimizing raw material mixing is essential for achieving higher output in SSP production. Using advanced mixing equipment, maintaining the correct ratios, ensuring uniform particle size distribution, and implementing automated monitoring systems can significantly enhance production efficiency. Additionally, temperature control and the use of additives help maintain a smooth and consistent mixing process.
By adopting these strategies, fertilizer manufacturers can achieve higher productivity, reduce waste, and meet the growing demand for SSP fertilizers. A well-optimized production line not only ensures higher output in SSP production but also improves product quality, contributing to sustainable agricultural practices.
Latest Articles & Tips
More-
03/14
OEM Fertilizer Equipment Manufacturing: Custom Solutions for Your Production Needs
read more -
02/27
Fertilizer Granulation for DAP and MAP: Enhancing Efficiency in Fertilizer Production
read more -
02/27
Fertilizer Production Solutions: Optimizing Efficiency and Sustainability in Fertilizer Manufacturing
read more -
02/13
Chemical Fertilizer Production Line: Enhancing Agricultural Productivity with Precision Manufacturing
read more
Send a message to us