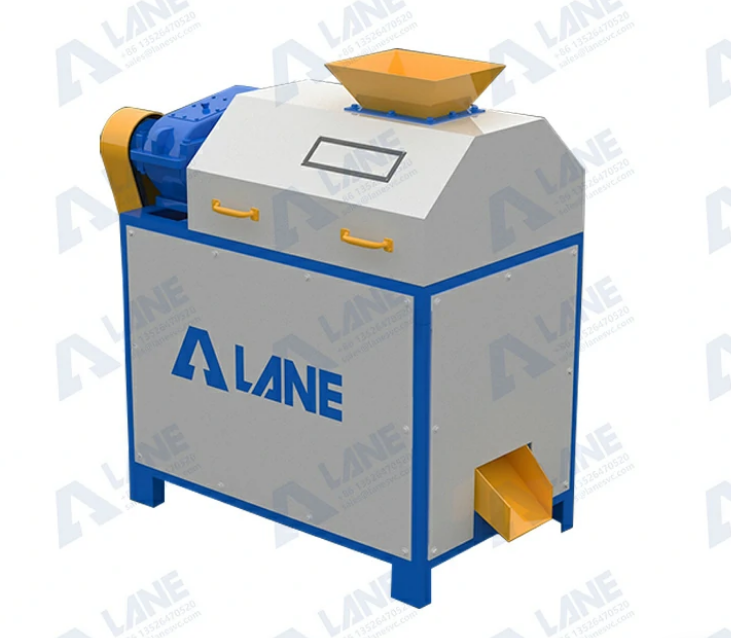
Double Roller Granulator
A double roller granulator is a type of granulation equipment that compresses powdered raw materials into dense, uniform granules through mechanical pressure. Unlike other granulation methods that require moisture or heat, the double roller granulator works by squeezing the materials between two rotating rollers. The compaction force from the rollers shapes the materials into granules, which are then easily broken down into individual particles.
This dry granulation method is ideal for producing compound fertilizers, especially those that are sensitive to heat or moisture. The double roller granulator is widely used in the production of NPK fertilizers, bio fertilizers, and other compound fertilizers, offering a simple yet effective granulation process that saves both time and energy.
LANE Group’s Double Roller Granulator is designed to optimize every aspect of the granulation process, ensuring high efficiency and product quality:
- Raw Material Preparation: The process begins with the selection and preparation of raw materials, typically including powdered fertilizers, chemical additives, and other essential nutrients. These materials must be dry and finely ground to ensure effective granulation.
- Feeding into the Granulator: The prepared raw materials are fed into the granulator’s hopper. The material then enters the space between the two counter-rotating rollers.
- Compaction and Granulation: As the material passes between the rollers, it is compressed under high pressure, forming a dense sheet of material. The rollers are designed with grooves or molds that shape the material into uniform granules as it is compacted.
- Granule Formation and Breaking: After compaction, the material is broken down into individual granules. The granules are typically uniform in size and shape, making them ideal for even nutrient distribution in the soil.
Finish Product Display
Highlight the Advantage
- There is no need to add water during the granulation process, and there is no need to dry the granules afterthe granulation is completed, which greatly reduces drying costs.
- Applicable materials include powdered organic fertilizer, compound fertilizer, graphite, mineral powder,industrial salt, snow melting agent, fragrant beads, etc, Some coarse fiber materials can also be used.
- The roller skin can be customized, The material is high-chromium 13/304 stainless steel. After surface immersion plating treatment, the anti-corrosion and wear-resistant effect is quite good.
- A dispersing device can be added at the inlet and outlet to prevent raw materials and finished products fromsticking together, and a dispersing device can be added under the drum to prevent materials from sticking to the drum.
Quality Assurance (QA)
Latest Articles & Tips
More-
12/05
MAP Fertilizer Processing Plant: Maximizing Resource Efficiency in Phosphorus Production
read more -
09/27
Phosphate Fertilizer Production Lines: The Hidden Force Behind Global Food Security
read more -
09/19
Ammonium Phosphate
read more -
09/09
read moreGlobal Potassium Sulfate Demand Growth: The Importance of Sulphate of Potash Production Line Equipment Selection